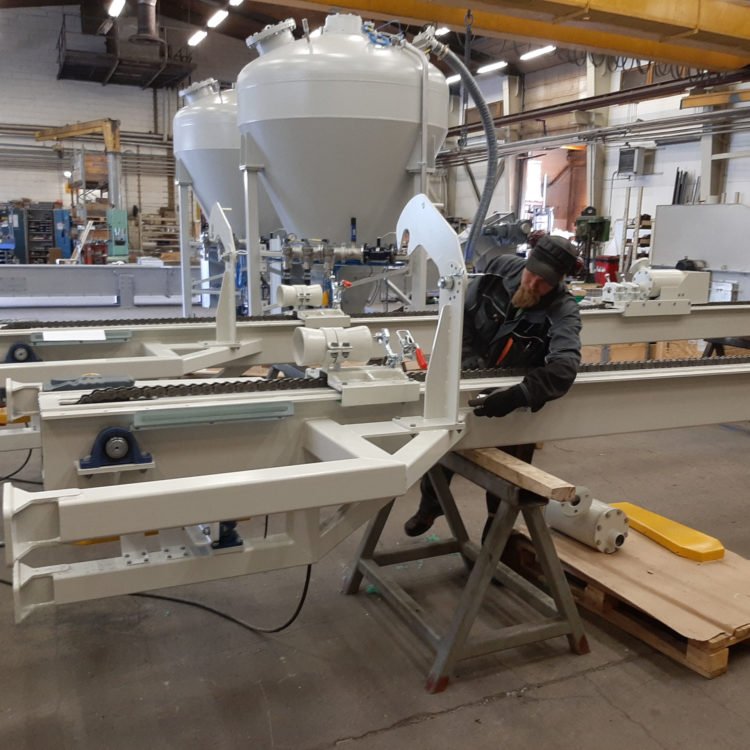
Pneumatic Conveying / Pressure Injection
Pressure Injection Systems for Smelters
At Kopar, we specialise in advanced pressure injection systems designed to enhance the efficiency and effectiveness of smelting processes. Our injection system is engineered to handle the most challenging conditions, ensuring optimal performance and reliability.
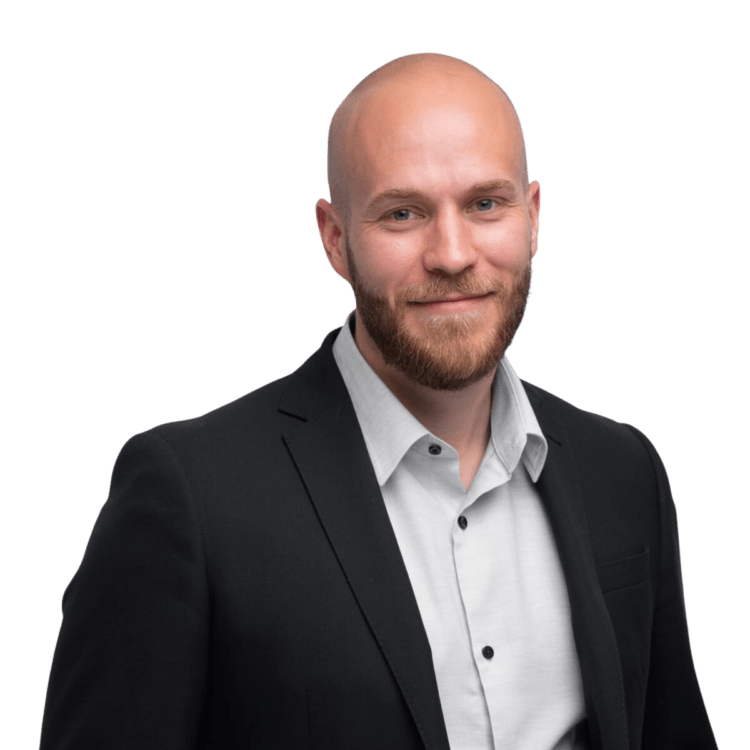
Innovative Solutions for Metal Recovery
Our pressure injection systems are particularly beneficial in the recovery of valuable metals. By injecting sulfur-rich concentrate into electric furnace, we modify metal chemistry resulting in lower liquidus point of the matte and thus increase metal recovery rates and improve flexibility of the tapping operations. This process is crucial for enhancing the overall efficiency of smelting operations.
Another example is the injection of fluxing materials (such as silica, or soda-lime mixture) into the copper melt to remove impurities such as lead and arsenic in the copper fire refining process.
Pressure injection is a unique system that combines scales, a feeder, and specially developed control automation with a pressure conveyor. This equipment ensemble, along with high transport pressure and an injection lance, enables the injection of material into molten material.
Key Features of Kopar's Pressure Injection Systems
- Advanced pneumatic transport: The system is based on proven high-pressure transport technology, ensuring efficient material handling even in the most demanding environments.
- Robust Equipment: Designed to withstand high temperatures and abrasive conditions, our pressure injection systems feature durable components such as pressure vessels, rotary valves, and movable injection lances
- Precise Control: With adjustable height mechanisms and sophisticated control systems, our pressure injection equipment allows for precise and consistent injection of materials into the molten bath
- Proven Technology: Kopar's pressure injection systems have been successfully implemented in various smelters worldwide
Watch video on YouTube.
Sulfurization Process
Electric furnace matte is naturally poor in sulphur. By modifying the sulfur content in the electric furnace matte, we can lower the liquidus temperature and viscosity, thereby reducing metal losses in the discarded slag. Additionally, this approach helps maintain a lower operating temperature, which is beneficial for extending the furnace lining's lifetime.
A pressure injection process (submerged lancing process) by Kopar can be applied to increase the sulphur content in electric furnaces.
Here's how the sulfurization process works:
- Sulphur addition: To enhance the recovery of valuable metals, sulphur is added to the electric furnace matte. This is achieved by injecting high sulfur-containing concentrate underneath the molten bath using a pressure injection system.
- Injection Equipment: The system consists of a storage vessel, pressure vessel, rotary valve, partially flexible conveying piping, and an injection lance. The pressure vessel is filled with concentrate and pressurised to ensure efficient injection.
- Lancing system: The injection lance is submerged into the molten slag, and the concentrate is injected below the surface. The lance height is adjustable to ensure precise positioning within the slag.
- Operational parameters: The injection process is carefully controlled, with parameters such as pressure and feed rate being monitored and adjusted to maintain optimal conditions. The system is designed to handle high temperatures and abrasive conditions, ensuring reliable operation.
- Benefits: By increasing the sulphur content in the electric furnace, the process improves slag chemistry, reduces operational temperatures, and enhances metal recovery. This results in lower metal losses in the waste slag and extends the furnace lining's lifetime.
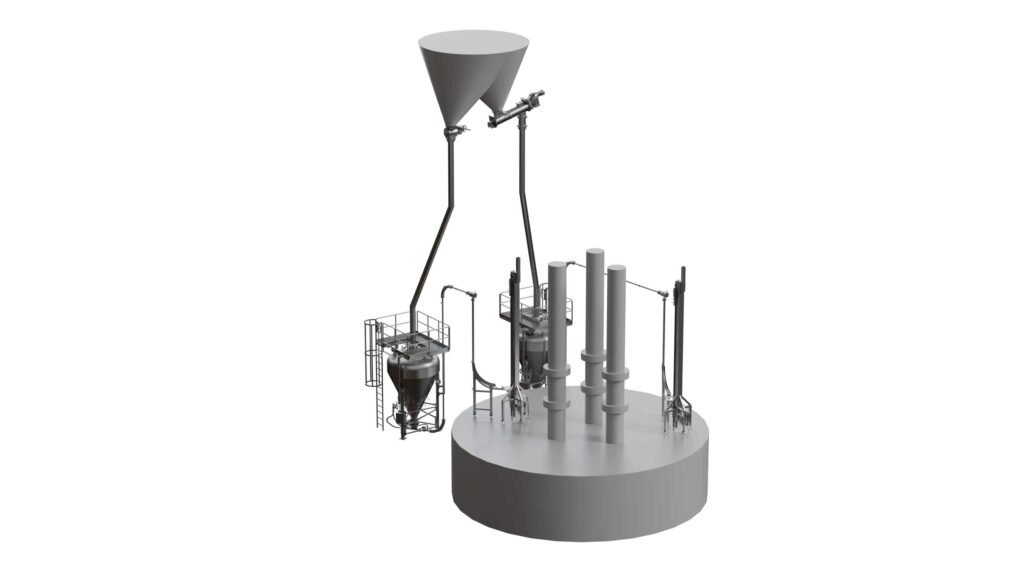
Why choose Kopar?
In summary, Kopar's pneumatic conveying systems offer significant advantages for smelting operations:
- Enhanced Metal Recovery: By improving slag chemistry and reducing operational temperatures, the sulfurization process by pressure injection facilitates the recovery of valuable metals.
- Versatile Applications: In larger context pneumatic conveying systems efficiently handle various materials such as concentrates, feed mixes, flux materials, WHB dusts, ESP dusts, and crushed slags.
- Cost-Effective Operations: The low air consumption and high system availability minimize operational expenses, making the process economically viable.
With over 30 years of experience in the industry, Kopar is a trusted name in pneumatic conveying and pressure injection systems. Our commitment to innovation, quality, and customer satisfaction sets us apart. Partner with us to optimise your smelting operations and achieve superior metal recovery.
Test how Kopar pneumatic conveying products fit your production plans
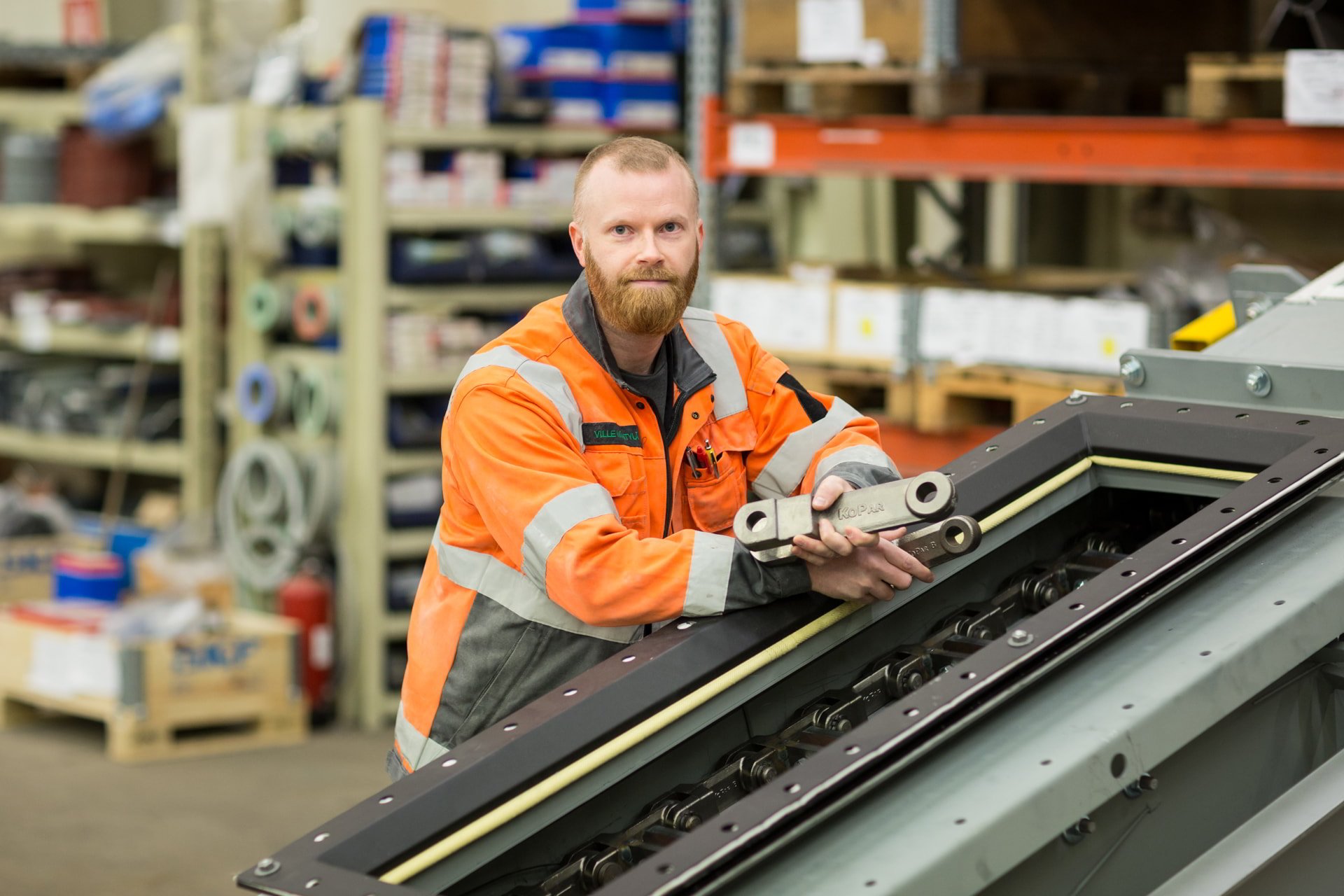
You have a challenge that needs solving?
Let us help! Contact us for more information about our products and services.