Enhanced durability in harsh conditions
Industrial environments are often characterized by extreme conditions that can quickly wear down conveying systems. Forged conveyor chains are designed to withstand these harsh environments, ensuring continuous operation without frequent maintenance or replacement. The materials used in these chains, such as case-hardened manganese steel or boron steel, are selected for their ability to resist abrasion, heat, and chemical corrosion. This resilience translates to a reliable performance even in the most demanding of applications.
At Kopar, we understand that the durability of conveyor chains is paramount. That's why we focus on providing chains that are not only robust but also tailored to the specific needs of your operation. Whether you're dealing with high temperatures or abrasive materials, our chains are engineered to maintain their integrity, ensuring that your conveying system remains operational for as long as possible without the need for constant intervention.
Optimised for Operational Efficiency
Efficiency is a key factor in any industrial process, and the performance of your conveyor chain can have a significant impact on your overall operational costs. Forged conveyor chains are designed to offer superior strength and reliability, which in turn reduces the frequency of downtime due to maintenance or repairs. This means that your processes can run smoother and more efficiently, with less interruption and greater output.
Our approach at Kopar is to provide conveyor chains that are not just strong, but also optimized for your specific operational needs. By customizing the type of link, the amount and location of flights, and other key characteristics, we ensure that your conveyor chain is as efficient as possible. This attention to detail helps to minimize operational expenses (OPEX) and, ultimately, the total cost of ownership of your conveying system.
Customization for Specific Material Handling Needs
Every material handling scenario is unique, with different materials requiring different conveying solutions. Forged conveyor chains offer the flexibility to be customized to the specific requirements of the material being transported. This customization ensures that the chain is perfectly suited to the task at hand, whether it requires a particular type of link, flight pitch, or chain width.
We pride ourselves on our ability to tailor-make industrial chains that not only meet the demands of your process but also contribute to the lowest possible total cost of ownership. By taking into account the characteristics of the material you need to convey, we can design a chain that optimizes both performance and cost-efficiency, ensuring that you get the most out of your investment.
Proactive Maintenance and Chain Longevity
Proactive maintenance is essential for maximizing the service life of your conveyor chain and preventing unplanned downtime. Forged conveyor chains are designed to be robust, but regular monitoring for signs of wear, such as elongation, is crucial. By anticipating maintenance needs, you can plan for replacements at the most opportune times, ensuring that your conveyor system continues to operate smoothly.
At Kopar, we have developed practical tools to help you measure chain elongation easily and frequently. This proactive approach to maintenance not only extends the life of the chain but also minimizes the risk of breakage and unplanned corrective maintenance. By recommending chain and sprocket replacements at the right time, we help you maintain optimal operation and avoid costly interruptions to your process.
Material Selection for Cost-Effective Solutions
While the initial purchase price of a conveyor chain is an important consideration, it is the total cost of ownership that truly reflects the value of your investment. Forged conveyor chains made from materials like boron steel may have a higher upfront cost compared to traditional manganese steel chains, but their extended service life can lead to significant savings over time. By reducing the need for frequent replacements, these chains offer a cost-effective solution in the long run.
We at Kopar are committed to helping you understand the long-term benefits of selecting the right materials for your conveyor chains. By choosing chains that are slightly more expensive upfront but offer multiple lifetimes of service, you can achieve huge savings in both money and time resources. Our focus on tempering steel with boron addition is a testament to our dedication to providing durable solutions that make financial sense for our clients.
Adaptability to Extreme Temperatures and Chemical Conditions
Some industrial processes expose conveyor chains to extreme temperatures or harsh chemical conditions that can quickly degrade lesser materials. Forged conveyor chains are available in specialized steel grades, such as heat-resistant steel and stainless steel, to withstand these challenging environments. This adaptability ensures that the chains can maintain their performance and structural integrity even under the most severe conditions.
Our expertise at Kopar extends to providing conveyor chains that are capable of operating in temperatures up to 700°C or in environments with harsh chemical exposure. By selecting the appropriate material, such as AISI 420 stainless steel for chemical resistance or 1.4713 heat-resistant steel for high-temperature applications, we ensure that your conveyor system remains reliable and efficient, regardless of the operating environment.
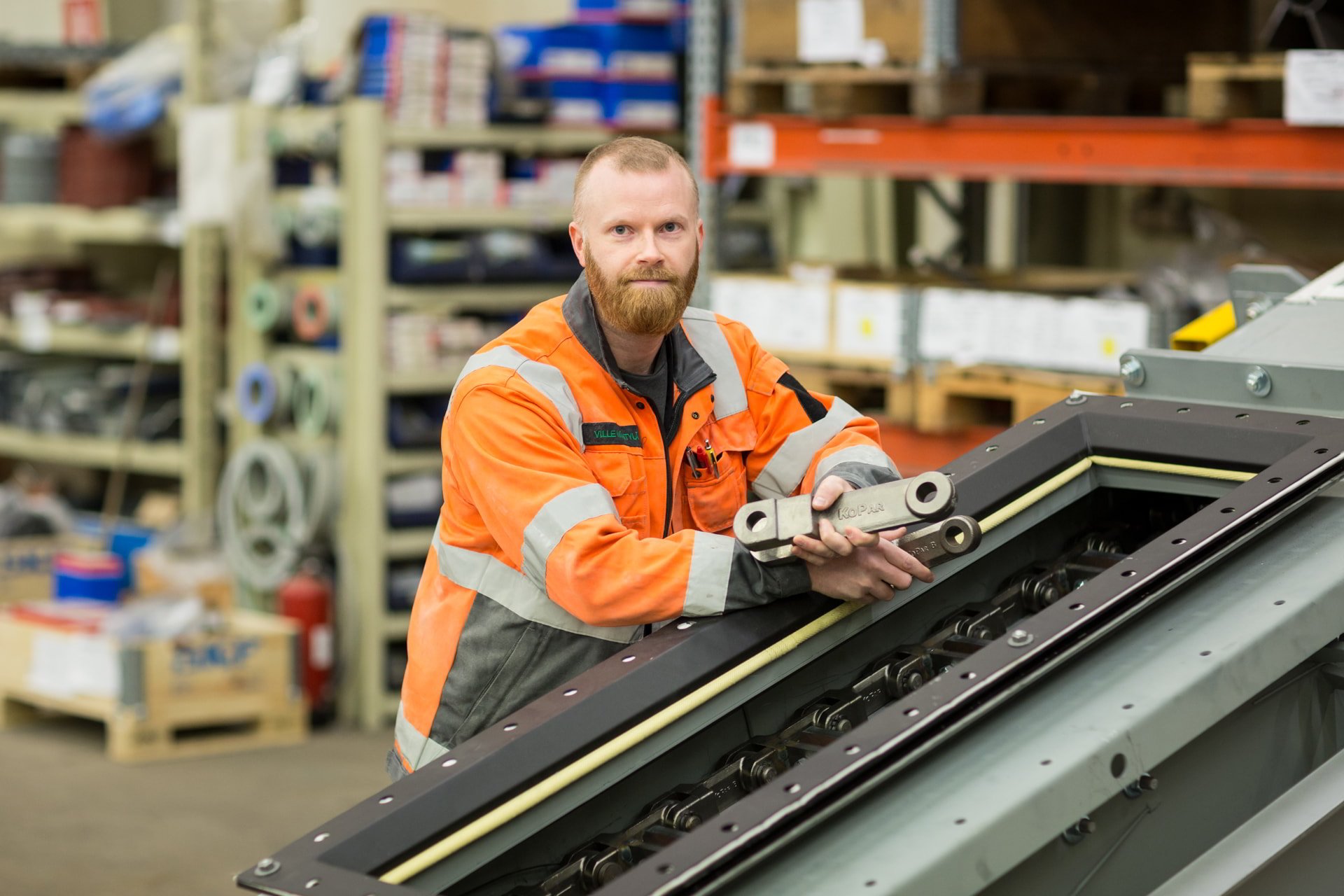
You have a challenge that needs solving?
Let us help! Contact us for more information about our products and services.