Introduction to Rotary Valves
Rotary valves, also known as rotary airlocks or rotary feeders, are essential components in various industrial applications. They are primarily used to control the flow of bulk materials from one chamber to another while maintaining a consistent airlock. This functionality is crucial in industries such as mining, cement, and chemical processing, where the precise handling of materials is necessary for efficient operations.
These valves consist of a rotor with multiple vanes that rotate within a housing. As the rotor turns, the vanes create pockets that capture and release material, allowing for controlled and continuous flow. Understanding the mechanics and applications of rotary valves can help industries optimise their material handling processes, ensuring both efficiency and safety.
Basic Components and Design
The primary components of a rotary valve include the rotor, housing, end plates, and drive mechanism. The rotor is typically a cylindrical drum with multiple vanes or blades that create pockets for material. The housing encases the rotor and provides the inlet and outlet ports for material flow. End plates seal the rotor ends, preventing material leakage and maintaining the airlock.
The drive mechanism, often an electric motor, powers the rotor's rotation. The design of the rotor and housing can vary based on the specific application, with considerations for material type, flow rate, and operating conditions. For instance, rotors can be made from various materials, including stainless steel and cast iron, to withstand abrasive or corrosive environments.
Operational Principles
Rotary valves operate on a simple yet effective principle. As the rotor turns, material enters the pockets through the inlet port. The rotation then carries the material to the outlet port, where it is discharged. This continuous rotation ensures a steady flow of material, which is crucial for maintaining consistent process conditions.
The airlock function is a key aspect of rotary valves. By maintaining a seal between the inlet and outlet, the valve prevents air or gas from passing through, which is essential in pneumatic conveying systems. This airlock capability helps maintain system pressure and prevents contamination or loss of material.
Applications in Pneumatic Conveying Systems
In pneumatic conveying systems, rotary valves play a critical role in feeding bulk materials into the conveying line. These systems use air or gas to transport materials through pipelines, and the rotary valve ensures a controlled and consistent feed rate. This is particularly important in applications where precise material handling is required, such as in the chemical and mineral industries.
Rotary valves can handle a wide range of materials, from fine powders to coarse granules. Their ability to maintain an airlock while feeding material into the conveying line helps optimize system efficiency and reduce energy consumption. Additionally, the robust design of rotary valves allows them to operate under high pressure and temperature conditions, making them suitable for demanding industrial environments.
Material Handling and Flow Control
Rotary valves are versatile tools for material handling and flow control in various industrial processes. They can be used to regulate the flow of materials from storage bins, hoppers, or silos into processing equipment. By adjusting the rotor speed, operators can control the feed rate, ensuring that the downstream process receives the right amount of material.
This flow control capability is essential in applications where precise dosing or batching is required. For example, in the cement industry, rotary valves are used to feed raw materials into kilns, ensuring a consistent and controlled flow. Similarly, in the chemical industry, they help manage the flow of powders and granules into reactors or mixers, optimizing the production process.
Maintenance and Durability
Regular maintenance is crucial for ensuring the reliable operation of rotary valves. This includes inspecting the rotor and housing for wear and tear, checking the seals and bearings, and lubricating the drive mechanism. Proper maintenance helps prevent material leakage, reduces downtime, and extends the service life of the valve.
Durability is another important consideration in the design and selection of rotary valves. Depending on the application, valves may be exposed to abrasive or corrosive materials, high temperatures, or high pressures. Selecting the right materials and design features, such as wear-resistant coatings or hardened rotors, can enhance the valve's durability and performance in challenging environments.
Advantages and Limitations
Rotary valves offer several advantages in industrial applications. They provide precise control over material flow, maintain an effective airlock, and can handle a wide range of materials. Their robust design allows them to operate under demanding conditions, making them suitable for various industries.
However, there are also some limitations to consider. Rotary valves can be prone to wear and tear, especially when handling abrasive materials. Regular maintenance is required to ensure reliable operation and prevent material leakage. Additionally, the initial cost of rotary valves can be higher compared to other types of feeders, but their performance and durability often justify the investment.
Conclusion
Rotary valves are indispensable components in many industrial applications, providing reliable and efficient material handling and flow control. Their ability to maintain an airlock while feeding materials into conveying systems makes them essential for optimizing process efficiency and reducing energy consumption. By understanding the design, operation, and maintenance of rotary valves, industries can enhance their material handling processes and achieve better operational outcomes.
As a company committed to innovation and excellence, we strive to provide our clients with the best solutions for their material handling needs. Our expertise in rotary valve technology and pneumatic conveying systems allows us to deliver customized solutions that meet the unique requirements of each application. By focusing on quality, reliability, and performance, we help our clients achieve their operational goals and maintain a competitive edge in their industries.
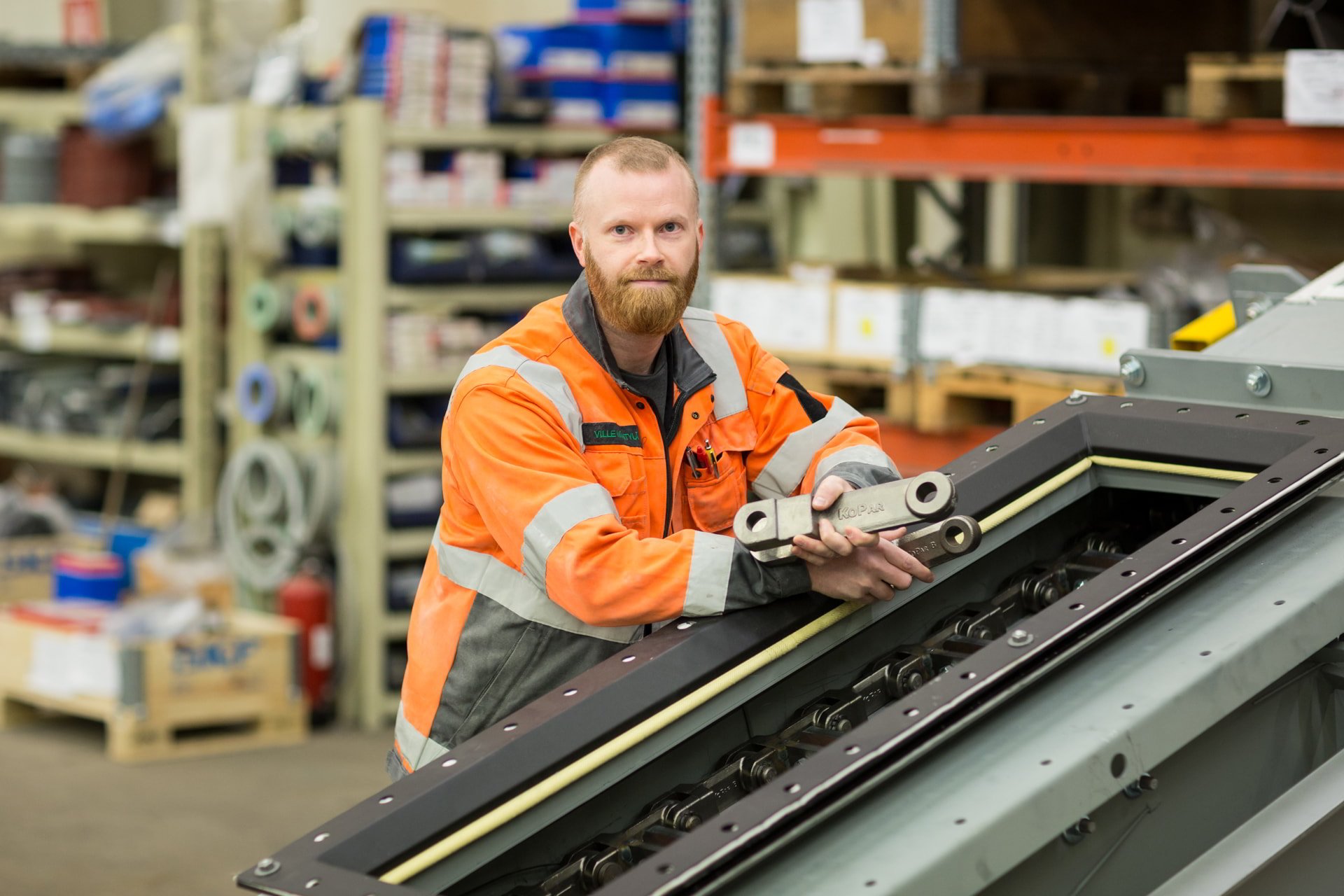
You have a challenge that needs solving?
Let us help! Contact us for more information about our products and services.