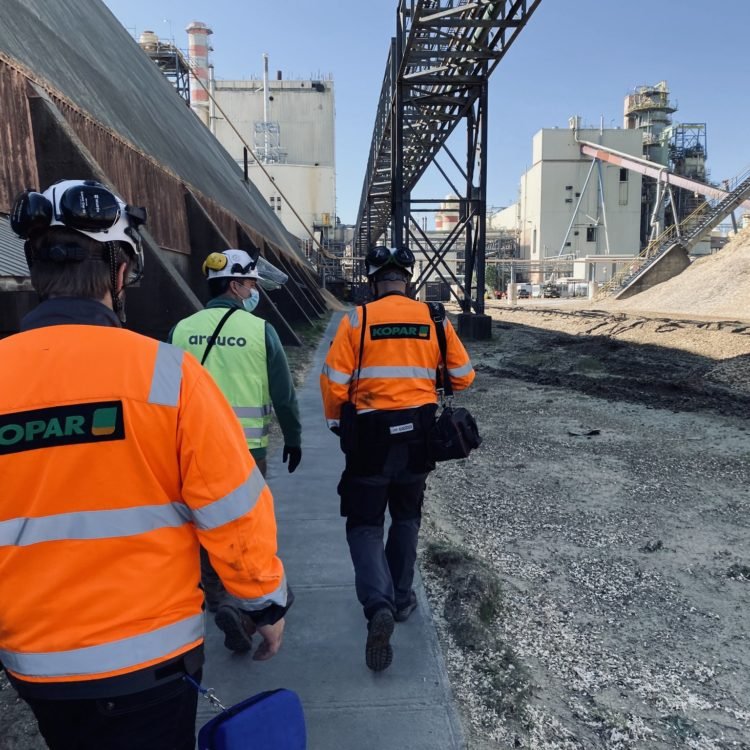
REFERENCES / MAINTENANCE IN SOUTH AMERICA
There is huge demand for maintenance services in South America
Whenever a machine malfunctions or a process does not run as it should, maintenance customers around the world turn to Kopar. System audits reveal how faults in process equipment can be prevented.
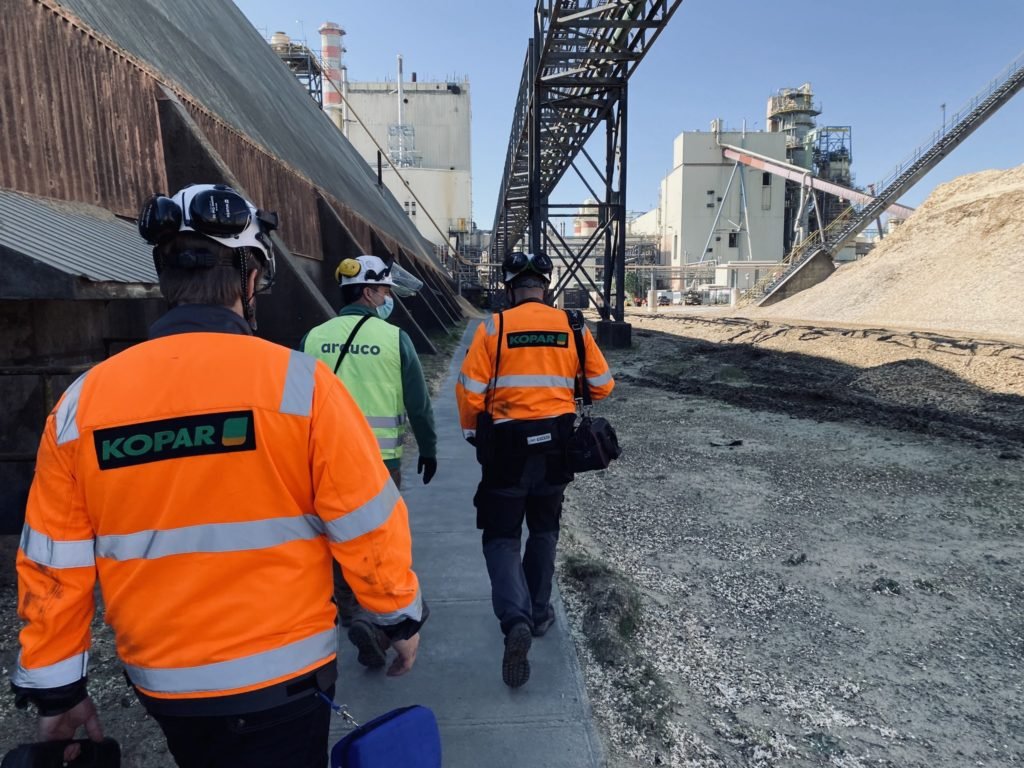
Kopar's Service team is well aware
that there is a growing demand for maintenance and consultancy services.
For example customers in South America
are looking for high-quality services,
for which we have the expertise and
parts to help them however challenging
the situation.
In Chile Kopar has conducted system audits and reviews in pulp mills and smelters whose drag chain conveyors, elevators and pneumatic conveyors were not working properly.
Similar serviced are naturally offered in other locations too, even closer to Finland.
The audits consist of inspecting the equipment as well as interviewing the operators and maintenance engineers. Conclusions are then drawn and a review report with recommended action plans presented to the customer.
"We were really satisfied with the Kopar team here in Brazil. Their knowhow was excellent and the team worked hard to be on schedule. We also got hints on day-to-day maintenance and have received support in adjustments even after the service work was completed."
Nathalia Brancagliao, AkzoNobel's Production Engineer
Service team in Brazil
Kopar's maintenance
expertise has also been needed in Brazil where the customer AkzoNobel at Veracel's pulp mill in Porto Seguro had an issue with a
leaking tabletop filter, which had originally been commissioned in 2004.
The process started with an inspection on this process crucial piece of equipment and a maintenance plan based on the inspection.
As this particular device is rare and highly specialised, the customer wanted Kopar there in person to perform the recommended maintenance work. There was no-one capable of fixing the device locally.
The timescale for repairing the filter
was tight, as the plant was only out of
action for six days.
Kopar had shipped the necessary parts
from Finland to Brazil in advance, which
meant that they were already waiting
there when the team arrived. Risks
had been minimised by sending more
parts than were needed.
Preparation is the key to successful projects, especially in service and maintenance since often times there are all kinds of surprises inside the device once it is opened.
"We always plan ahead and try to
think of all the things that we might need
on site. The further we travel from Finland,
the more important it is to prepare for all
eventualities." comments Kopar's Service Manager Ville Mäntylä.
However this Brazilian project ran relatively smoothly, and the few little surprises that were encountered were overcome with the customer's help.
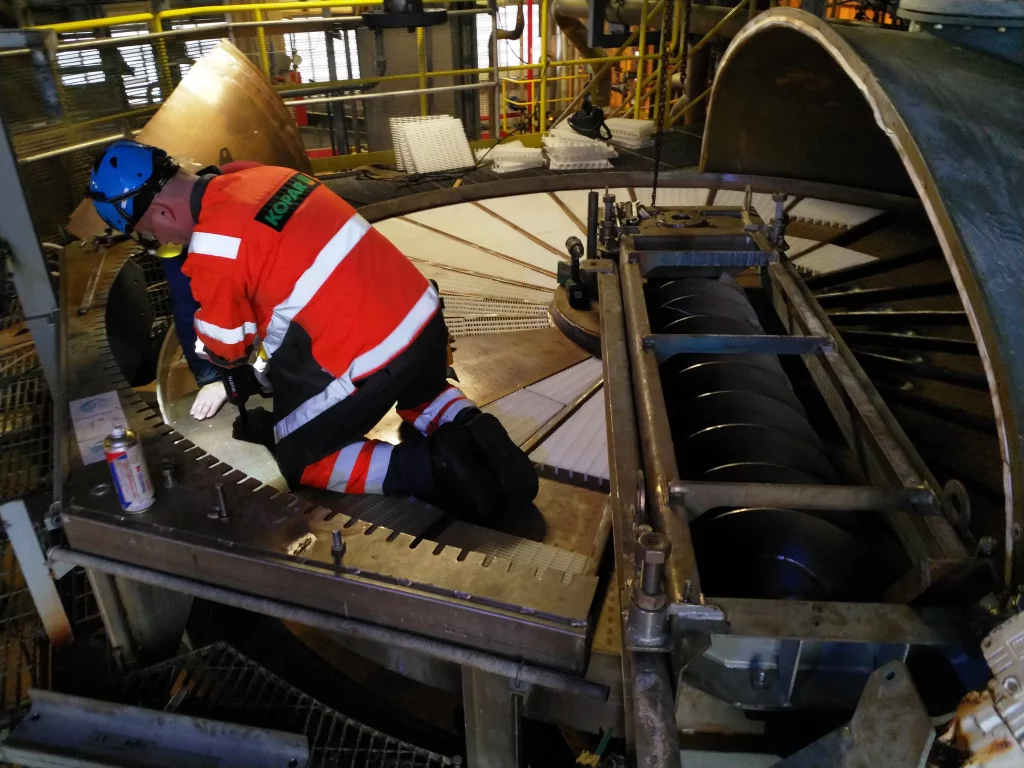
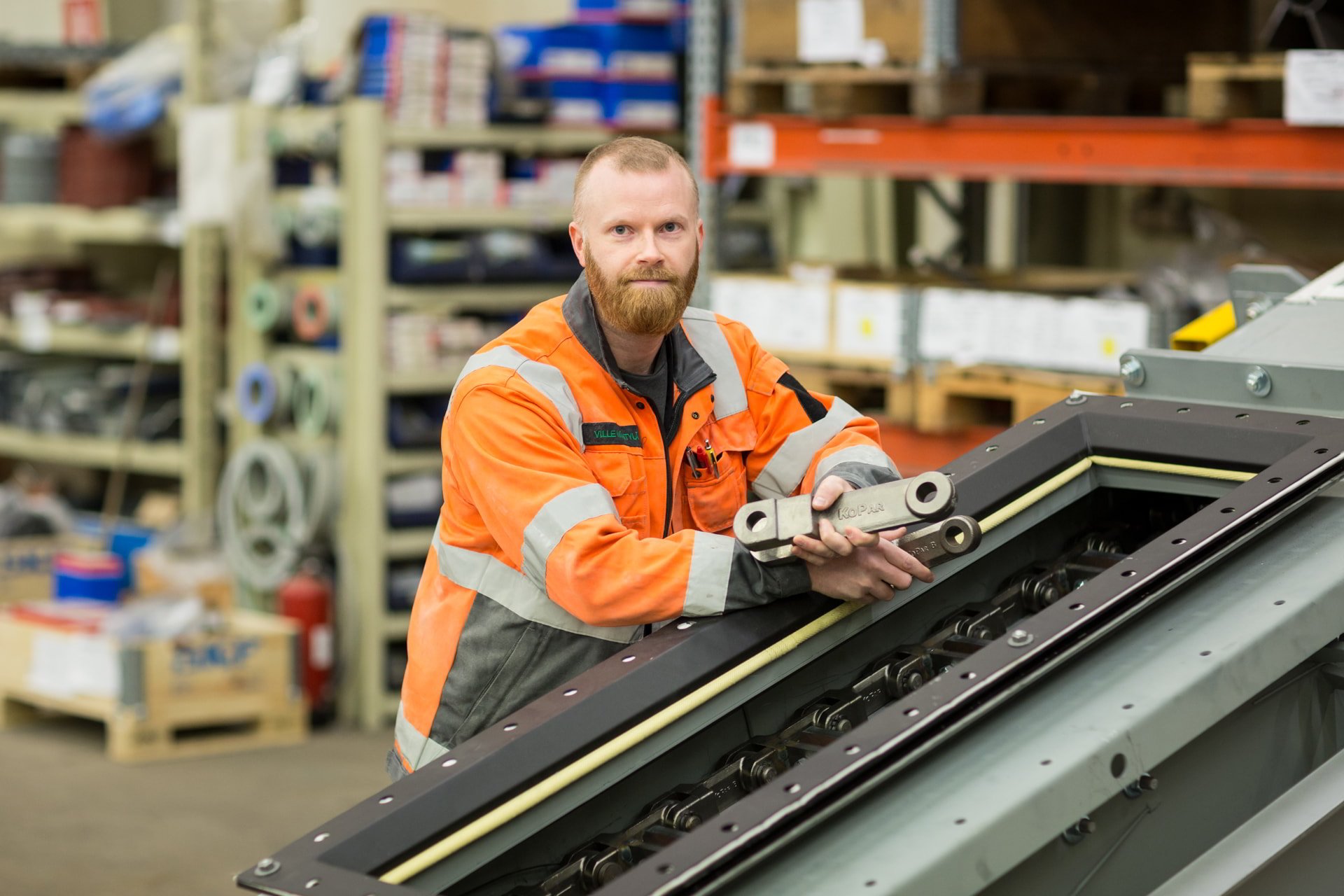
You have a challenge that needs solving?
Let us help! Contact us for more information about our products and services.