Pneumatic Conveying Systems
Pneumatic conveying systems are a highly efficient method for transporting bulk materials through pipelines using air pressure. These systems are particularly useful for industries that handle fine powders, granules, and other small particles. The primary advantage of pneumatic conveying is its ability to move materials over long distances with minimal spillage and contamination.
There are two main types of pneumatic conveying: high-pressure and low-pressure systems. High-pressure systems, also known as dense phase conveying, are ideal for transporting abrasive or fragile materials over long distances. Low-pressure systems, or dilute phase conveying, are better suited for softer materials that require high velocity for efficient transport. Both systems can be customized to meet the specific needs of a business, ensuring optimal performance and cost-effectiveness.
Hydraulic Conveying Systems
Hydraulic conveying systems use water or other liquids to transport materials through pipelines. This method is particularly effective for moving heavy, coarse materials such as coal, gravel, and sand. Hydraulic systems are known for their ability to handle large volumes of material with minimal energy consumption, making them a cost-effective solution for many industries.
One of the key benefits of hydraulic conveying is its ability to reduce dust and noise pollution, which can be significant concerns in industrial settings. Additionally, these systems can be designed to operate in both open and closed-loop configurations, providing flexibility for various applications. Proper maintenance and monitoring are essential to ensure the longevity and efficiency of hydraulic conveying systems.
Vacuum Conveying Systems
Vacuum conveying systems use negative pressure to move materials through pipelines. This method is particularly effective for handling lightweight, fine powders and granules. Vacuum systems are often used in industries where contamination and product loss must be minimized, such as the chemical and plastics industries.
One of the main advantages of vacuum conveying is its ability to transport materials in a controlled and enclosed environment, reducing the risk of contamination and spillage. Additionally, vacuum systems can be easily integrated into existing production lines, providing a seamless and efficient solution for material handling. Regular maintenance and monitoring are crucial to ensure the optimal performance of vacuum conveying systems.
Mechanical Conveying Systems
Mechanical conveying systems use mechanical components such as screws, chains, and buckets to transport materials through pipelines. These systems are ideal for handling a wide range of materials, including powders, granules, and bulk solids. Mechanical conveyors are known for their durability and ability to handle heavy loads, making them a popular choice for many industries.
There are several types of mechanical conveying systems, including screw conveyors, chain conveyors, and bucket elevators. Each type has its own unique advantages and is suited for specific applications. For example, screw conveyors are ideal for moving materials horizontally or at a slight incline, while bucket elevators are better suited for vertical transport. Proper maintenance and regular inspections are essential to ensure the longevity and efficiency of mechanical conveying systems.
Pipeline Design and Maintenance
Effective pipeline design and maintenance are crucial for ensuring the efficiency and reliability of any conveying system. Proper pipeline design involves selecting the appropriate materials, dimensions, and layout to meet the specific needs of a business. This includes considering factors such as material properties, transport distance, and environmental conditions.
Regular maintenance is essential to prevent issues such as blockages, leaks, and wear and tear. This includes routine inspections, cleaning, and replacing worn components as needed. Implementing a comprehensive maintenance plan can help businesses minimize downtime and ensure the long-term performance of their conveying systems.
Customization and integration
Customization and integration are key factors in ensuring the success of any pneumatic conveying solution. Each business has unique needs and requirements, and a one-size-fits-all approach is rarely effective. Customizing conveying systems to meet the specific needs of a business can help optimize performance, reduce costs, and improve overall efficiency.
Integration is also crucial for ensuring seamless operation and minimizing disruptions. This includes integrating conveying systems with existing production lines, control systems, and other equipment. Proper integration can help streamline operations, improve communication, and reduce the risk of errors and downtime. Working with experienced professionals can help businesses achieve the optimal level of customization and integration for their pneumatic conveying solutions.
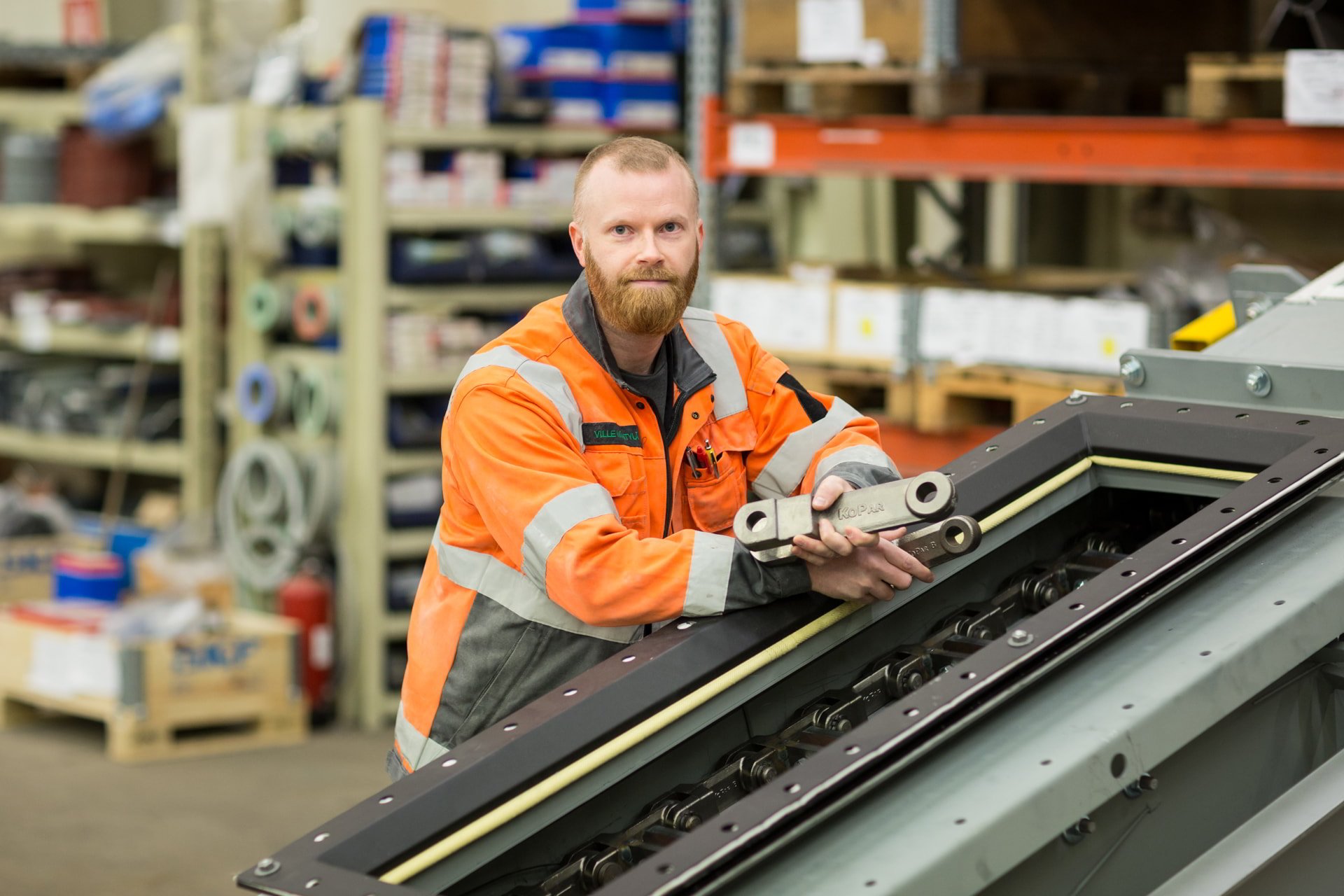
You have a challenge that needs solving?
Let us help! Contact us for more information about our products and services.