Understanding the Critical Role of Forged Conveyor Chains in the Process Industry
Conveying solid materials is a fundamental aspect of the process industry, where efficiency and reliability are paramount. Mechanical conveying, which encompasses horizontal and vertical movement, is a preferred method due to its effectiveness in handling challenging materials. Forged conveyor chains are at the heart of this system, providing the necessary strength and durability to move hot, abrasive, and dusty substances without faltering.
Our expertise in this area is well-recognised, with a focus on delivering solutions that withstand the most demanding conditions. The design of our drag chain conveyors, for instance, is smelter-proven, ensuring that they can withstand extreme environments where other conveyors might fail. This resilience is a testament to the quality of the forged chains that form the backbone of these systems.
Material Selection: The Foundation of Conveyor Chain Performance
Selecting the right material for conveyor chains is not just about durability; it's about ensuring the lowest operational costs and total cost of ownership. While case-hardened manganese steel is widely used for its affordability, a deeper analysis of total costs reveals that alternative materials, such as boron steel, offer significant advantages. Despite a higher initial purchase price, the extended service life of boron steel chains can lead to substantial savings in both financial and time resources.
We advocate for the use of tempering steel with boron addition due to its superior lifespan, which translates into clear benefits for users. For specialized applications, we also provide chains made from stainless steel for chemical resistance and heat-resistant steel for high-temperature operations, ensuring that our chains meet the specific needs of each process.
Maximizing Chain Lifespan Through Continuous Maintenance
Proactive maintenance is crucial for keeping drag chain conveyors operating smoothly and preventing unplanned downtime. We have developed tools and procedures that allow for easy and frequent measurement of chain elongation, a key indicator of wear. By monitoring this parameter, users can optimize the lifespan of their chains and reduce the likelihood of breakages that lead to corrective maintenance.
It is recommended to replace chains when elongation reaches a critical threshold, typically around 2.8%. At the same time, it is also advisable to replace the sprockets to maintain the optimal performance of the conveyor system. This approach to maintenance ensures that the conveyor operates at peak efficiency, contributing to the overall productivity of the process.
Design Versatility for Complex Environments
Our conveying solutions, including drag chain conveyors, screw conveyors, elevators, and excavators, are engineered with versatility in mind. They are capable of handling steep inclinations and are designed with a modular approach to fit into challenging spaces. This adaptability is essential for industries that operate in less-than-ideal conditions and require equipment that can be customized to their unique environment.
These systems are not only flexible in their installation but also in their capacity to handle large volumes of material, supporting up to 300 tons per hour. They can also operate at extreme temperatures, with some systems designed to withstand up to 600°C. This level of versatility ensures that our solutions can meet the diverse needs of the process industry.
Enhancing Operational Efficiency with Tailor-Made Solutions
Every process and condition presents its own set of challenges, which is why tailor-made industrial chains are essential. Customized chains ensure that the specific demands of a process are met, leading to optimized operational efficiency. By working closely with our clients, we can design chains that not only fit their requirements but also contribute to the lowest possible operational expenses.
Our commitment to providing tailor-made solutions extends to the selection of materials and the design of the chains themselves. By understanding the unique conditions of each application, we can recommend the most appropriate materials and configurations, ensuring that our clients receive conveyor chains that are precisely suited to their needs.
Conclusion
In the process industry, where the movement of materials is a constant and critical task, the quality of forged conveyor chains cannot be overlooked. These chains are the linchpins of mechanical conveying systems, tasked with moving heavy, hot, and abrasive materials day in and day out. By focusing on material selection, continuous maintenance, design versatility, and tailor-made solutions, we ensure that our conveyor chains meet the highest standards of performance and efficiency.
Understanding the intricacies of these systems and the environments they operate in allows us to provide solutions that not only meet but exceed the expectations of our clients. With a commitment to innovation and quality, we continue to support the process industry with conveyor chains that are built to last under the toughest conditions.
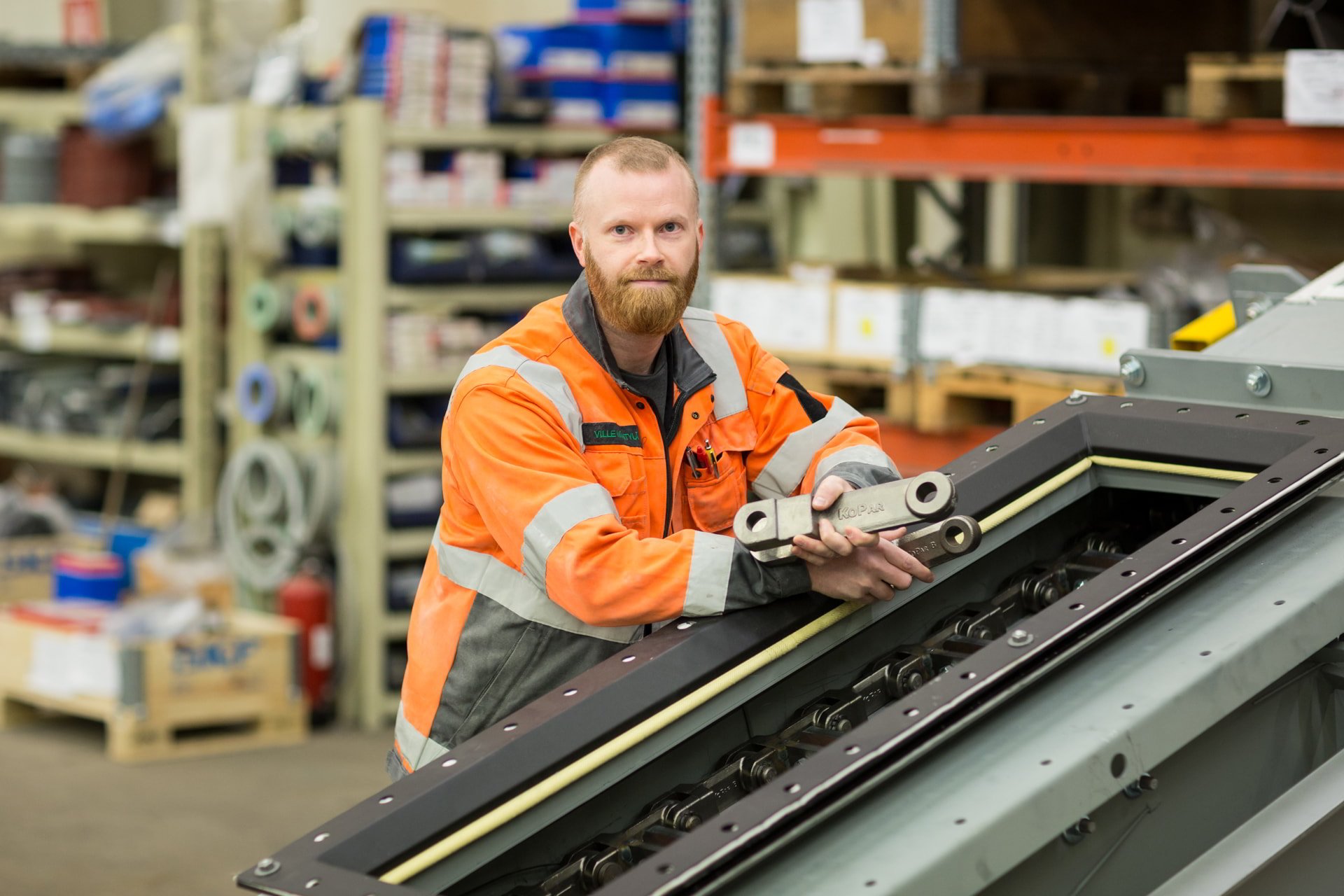
You have a challenge that needs solving?
Let us help! Contact us for more information about our products and services.