Introduction to Rotary Valves in Material Handling
Rotary valves are a critical component in the material handling processes across various industries. These devices are designed to control the flow of bulk materials from one chamber to another, ensuring a smooth and efficient transfer. Rotary valves are particularly essential in systems where materials need to be metered and fed into a process at a controlled rate. Their versatility and reliability make them indispensable in handling a wide range of materials, from fine powders to coarse granules.
In material handling, the primary function of rotary valves is to regulate the flow of materials while maintaining a pressure-tight seal between different sections of the system. This capability is crucial in preventing air leakage and ensuring the efficient operation of pneumatic conveying systems. By understanding the role and functionality of rotary valves, industries can optimize their material handling processes, leading to increased efficiency and reduced operational costs.
How Rotary Valves Work
Rotary valves operate by rotating a vaned rotor inside a housing. As the rotor turns, it creates pockets that capture and release material in a controlled manner. The rotation speed and the size of the pockets determine the flow rate of the material being handled. This precise control over material flow is essential in applications where consistent feeding and metering are required.
The design of rotary valves allows them to handle a variety of materials, including abrasive, sticky, and fibrous substances. The materials used in constructing the valves, such as stainless steel or cast iron, are chosen based on the specific requirements of the application. Additionally, the rotor and housing can be coated with wear-resistant materials to extend the valve's service life and maintain its performance under harsh conditions.
Applications of Rotary Valves in Material Handling
Rotary valves are widely used in industries such as cement, mining, and chemical processing. In the cement industry, for example, rotary valves are used to control the flow of raw materials into the kiln and to manage the discharge of finished products. Their ability to handle abrasive materials makes them ideal for this application.
In the mining industry, rotary valves are employed to manage the flow of minerals and ores. These valves are designed to withstand the harsh conditions of mining operations, including exposure to dust, moisture, and extreme temperatures. By ensuring a consistent flow of materials, rotary valves help maintain the efficiency of mining processes and reduce downtime.
Benefits of Using Rotary Valves
One of the primary benefits of using rotary valves in material handling is their ability to provide precise control over material flow. This precision is essential in applications where accurate dosing and metering are required. By maintaining a consistent flow rate, rotary valves help ensure the quality and consistency of the final product.
Another significant advantage of rotary valves is their durability and reliability. These valves are designed to operate under challenging conditions, including high temperatures and abrasive materials. Their robust construction and wear-resistant coatings help extend their service life, reducing the need for frequent maintenance and replacement.
Challenges and Considerations
While rotary valves offer numerous benefits, there are also challenges and considerations to keep in mind. One of the primary challenges is ensuring that the valve is properly sized and configured for the specific application. An improperly sized valve can lead to issues such as material leakage, clogging, and reduced efficiency.
Another consideration is the maintenance of the rotary valve. Regular inspection and maintenance are essential to ensure the valve's continued performance and reliability. This includes checking for wear and tear, lubricating moving parts, and replacing worn components as needed. By maintaining the valve in good condition, industries can avoid costly downtime and ensure the smooth operation of their material handling processes.
Innovations in Rotary Valve Technology
Recent advancements in rotary valve technology have led to the development of more efficient and reliable valves. Innovations such as improved sealing mechanisms, wear-resistant coatings, and advanced materials have enhanced the performance and durability of rotary valves. These advancements have made it possible to handle a wider range of materials and operate under more demanding conditions.
Additionally, the integration of smart technology and automation has further improved the efficiency of rotary valves. Smart rotary valves can be equipped with sensors and control systems that monitor their performance in real-time. This allows for predictive maintenance and optimization of the material handling process, reducing downtime and improving overall efficiency.
Conclusion
Rotary valves play a crucial role in material handling processes across various industries. Their ability to provide precise control over material flow, combined with their durability and reliability, makes them an essential component in many applications. By understanding the functionality and benefits of rotary valves, industries can optimize their material handling processes, leading to increased efficiency and reduced operational costs.
As technology continues to advance, rotary valves will likely become even more efficient and versatile. Innovations in materials, design, and automation will further enhance their performance and expand their range of applications. By staying informed about these advancements, industries can continue to benefit from the advantages that rotary valves offer in material handling processes.
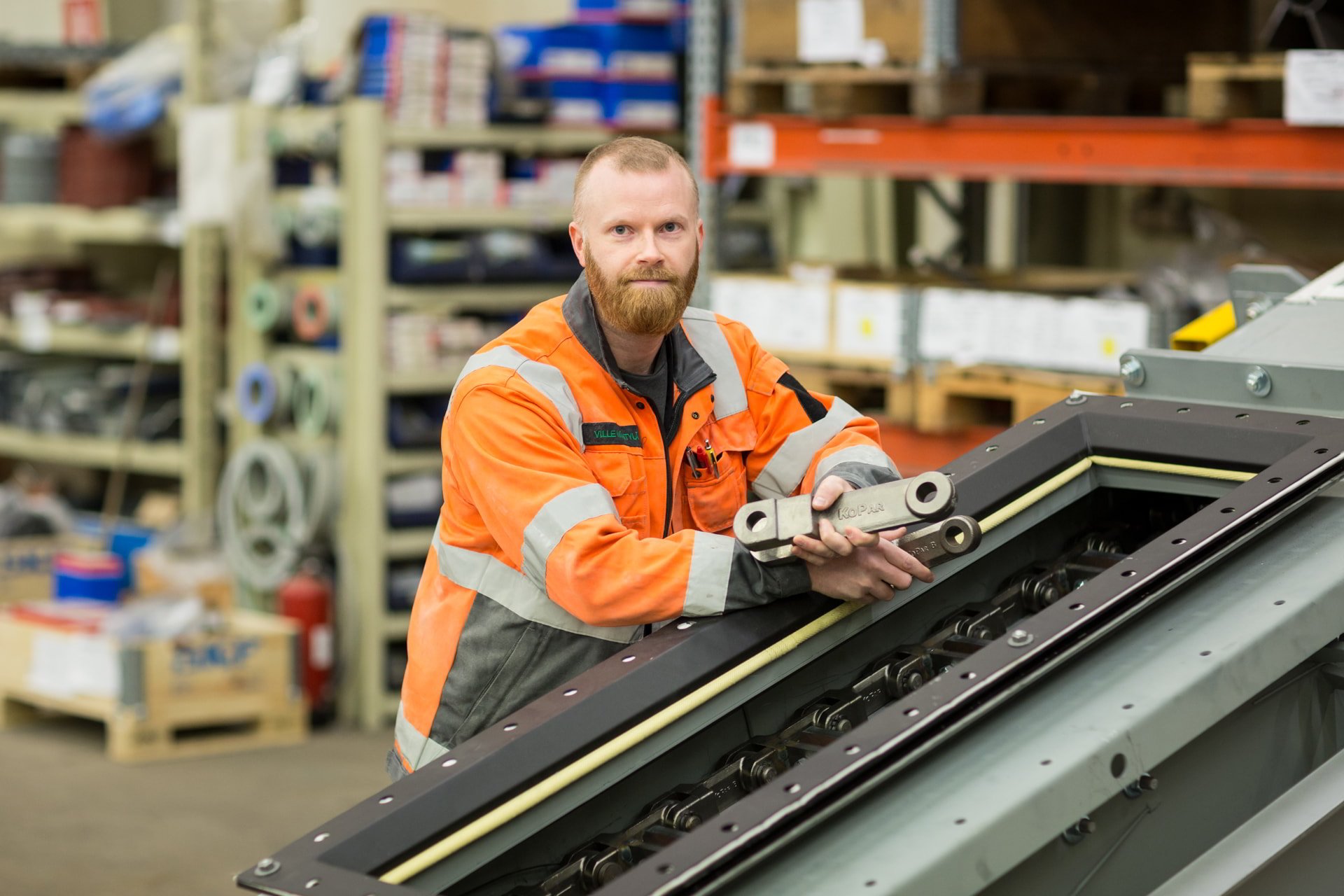
You have a challenge that needs solving?
Let us help! Contact us for more information about our products and services.