What is a chain conveyor and why is it important?
A chain conveyor is a central part of industrial material handling systems, designed to efficiently and safely transfer large amounts of material. Chain conveyors can be either horizontal, vertical, or inclined, which makes them versatile across various industries such as mining and construction. Their significance is particularly highlighted when a continuous flow of materials is needed to minimize downtime and improve productivity.
Choosing the right chain conveyor is a crucial decision affecting the efficiency of the entire production process. The correct chain conveyor can reduce production disruptions, enhance safety, and lower environmental impacts. The selection must be made carefully to ensure the optimal performance and durability of the conveyor system.
Industrial conveyor solutions, like chain conveyors, are especially important in processes where material handling is critical to maintaining smooth production. Chain conveyors can reduce the need for manual labour and improve workplace safety, making them essential components in modern industrial facilities.
What are the criteria for selecting a chain conveyor?
Several factors influence the selection of a chain conveyor, with capacity being one of the most important. It is essential to evaluate how much material the chain conveyor can handle within a certain time without compromising its performance. Proper capacity sizing ensures that the conveyor system can meet production needs both now and in the future.
The type of material greatly affects the choice of a chain conveyor. Different materials, such as sand, gravel, or chemicals, impose various requirements on the conveyor system. For example, the density, particle size, and temperature of the material being conveyed are important factors to consider in selecting the right chain conveyor.
The operating environment is the third major selection criterion. The conveyor solution must withstand environmental conditions such as humidity, dust, or extreme temperatures. Therefore, it is important to choose a chain conveyor with materials and structures suitable for enduring these demanding conditions.
How do maintenance and upkeep affect the choice of a chain conveyor?
The maintenance and upkeep of a chain conveyor are critical factors to consider in the selection process. A well-designed conveyor system reduces maintenance needs and extends its lifespan, making it a cost-effective solution in the long run. Regular maintenance ensures that the chain conveyor operates optimally and that potential issues can be addressed before they impact production.
The ease and availability of maintenance are also important factors. By choosing a chain conveyor that is easy to maintain and has readily available spare parts, downtime can be minimized, and production efficiency maximized. This is especially important in processes where downtime can cause significant financial losses.
In addition, the training and expertise of maintenance personnel should be considered when selecting a chain conveyor. Trained professionals can perform necessary maintenance tasks quickly and efficiently, reducing production downtimes and enhancing the overall reliability of the system.
What are the benefits of Kopar chain conveyors?
Kopar chain conveyors offer several advantages compared to other options available on the market. They are designed to withstand even the most demanding conditions, and their performance is superior. This means they can handle large amounts of material efficiently and safely, even at temperatures up to 700°C.
One of the most significant advantages of Kopar chain conveyors is the use of boron steel chains, which are considerably more durable than the more commonly used manganese steel chains. This improves the durability of the conveyor system and reduces maintenance needs, making them cost-effective solutions in the long term.
Kopar chain conveyors are also extremely safe to use. They can be designed for explosive environments, such as ATEX zones 21 and 22, which expands their applicability in various industrial applications. Additionally, they offer specialized solutions, such as water-cooled conveyors, which protect the system from thermal effects and enhance its durability.
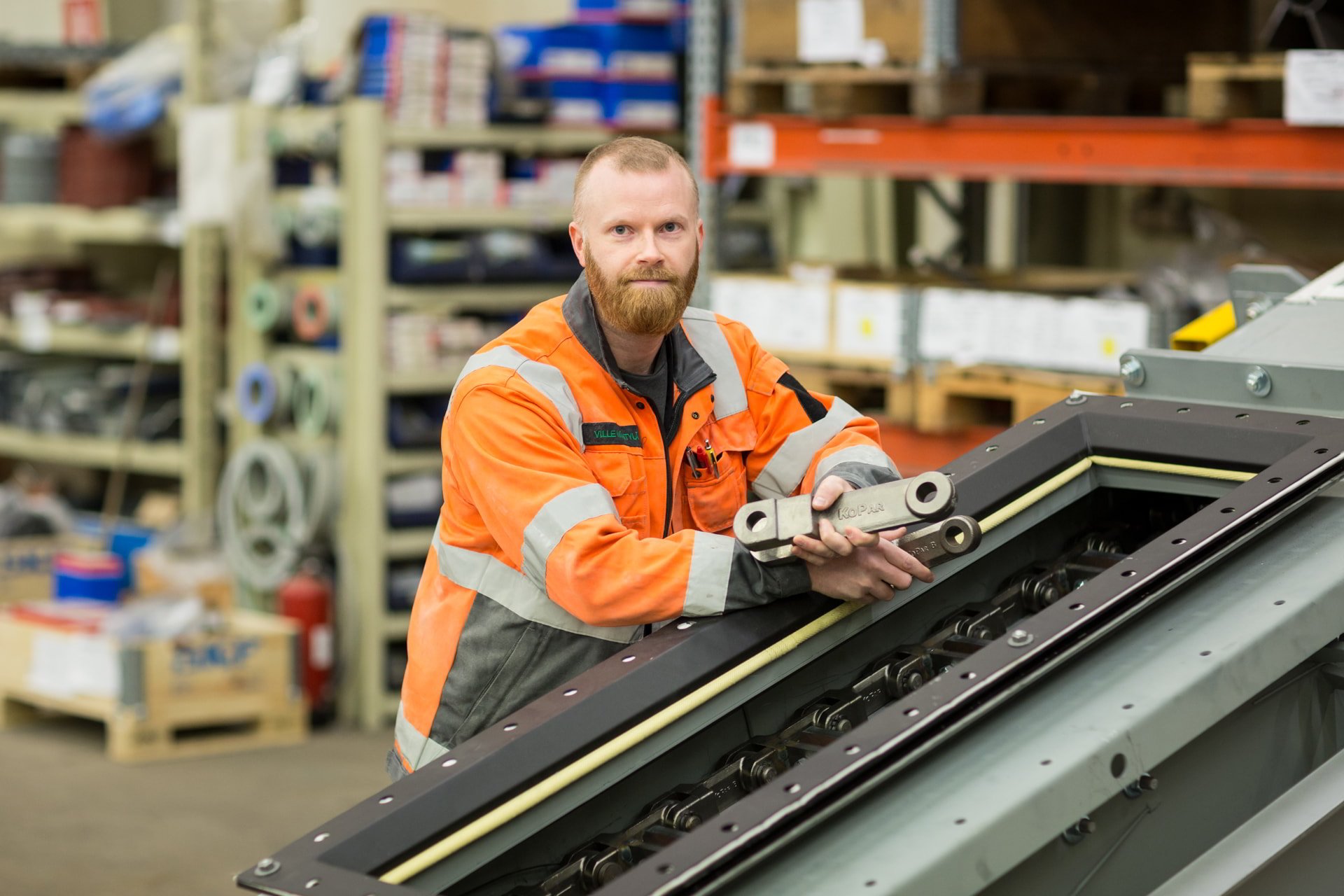
You have a challenge that needs solving?
Let us help! Contact us for more information about our products and services.