Understanding the Importance of Material Selection
When it comes to industrial applications, the choice of material for conveyor chains is paramount. The most common material used is case-hardened manganese steel (20MnCr5, EN 1.7147), primarily due to its cost-effectiveness. However, a deeper analysis into the total cost of ownership reveals that initial savings may be deceptive. We advocate for the use of boron steel (27MnCrB5, EN 1.7182) in our chains, as it offers multiple lifetimes compared to traditional materials, translating into significant savings over time.
For environments that are particularly harsh or have unique requirements, alternative materials such as stainless steel (AISI 420, EN 1.4034) or heat-resistant steel (1.4713) may be necessary. These materials are designed to withstand extreme chemical conditions or continuous operation at elevated temperatures, ensuring that your conveyor system remains reliable under any circumstances.
Calculating Total Ownership Costs
When selecting a forged conveyor chain, it's crucial to look beyond the purchase price. A comprehensive evaluation includes considering operational expenses (OPEX) and the total cost of ownership. While boron steel chains may have a higher upfront cost, their extended service life can result in lower long-term expenses due to reduced downtime and maintenance needs. This approach ensures that you are making a financially sound decision for your operation.
It's essential to factor in the frequency of replacements and the associated costs of downtime and labour. By choosing a chain that lasts longer, you can minimize these disruptions and maintain a more efficient and cost-effective operation. We focus on providing solutions that, while they may appear more expensive initially, offer substantial savings and improved performance in the long run.
Maintenance and Anticipation
Continuous maintenance is key to the smooth operation of drag chain conveyors. We have developed tools that allow for easy and frequent measurement of chain elongation, a critical indicator of wear. By monitoring elongation and adhering to recommended thresholds, such as replacing chains at 2.8% elongation, you can prevent unexpected breakdowns and extend the service life of your conveyor system.
It's also important to replace sprockets concurrently with the chains to ensure optimal performance. This proactive approach to maintenance helps to avoid unplanned corrective actions, keeping your process running efficiently and reducing the risk of costly downtime.
Customization for Specific Needs
Every industrial environment has its unique challenges, and a one-size-fits-all solution is rarely sufficient. We specialize in creating tailor-made industrial chains that are designed to meet the specific demands of your process and conditions. This customization ensures that you receive a product that not only fits your system perfectly but also operates at peak efficiency.
Whether you're dealing with hot, abrasive, or dusty materials, our conveyor solutions are engineered to handle the toughest conditions. Our expertise in the field allows us to design systems that are not only durable but also adaptable to various material handling scenarios, including steep inclinations and high-temperature environments.
Capacity and Temperature Considerations
When selecting a forged conveyor chain, it's important to consider the capacity and temperature requirements of your operation. Our systems are capable of handling large capacities, supporting up to 300 tons per hour, and can operate at temperatures as high as 600°C. These factors play a crucial role in determining the appropriate chain for your needs.
Ensuring that your conveyor chain can withstand the specific demands of your process is essential for maintaining efficiency and preventing premature wear. We provide solutions that are not only robust but also tailored to the unique thermal and capacity challenges of your industry.
Expertise in handling Challenging Materials
Our reputation is built on our ability to handle and convey materials that are hot, abrasive, and challenging. The drag chain conveyors we provide are smelter-proven, capable of withstanding conditions that would compromise other systems. This level of resilience is a testament to the quality and reliability of our products.
We offer a range of mechanical conveying solutions, including drag chain conveyors, screw conveyors, elevators, and excavators, all designed to meet the rigorous demands of the process industry. Our commitment to excellence ensures that we deliver conveyor systems that are not just durable but also optimized for your specific material handling needs.
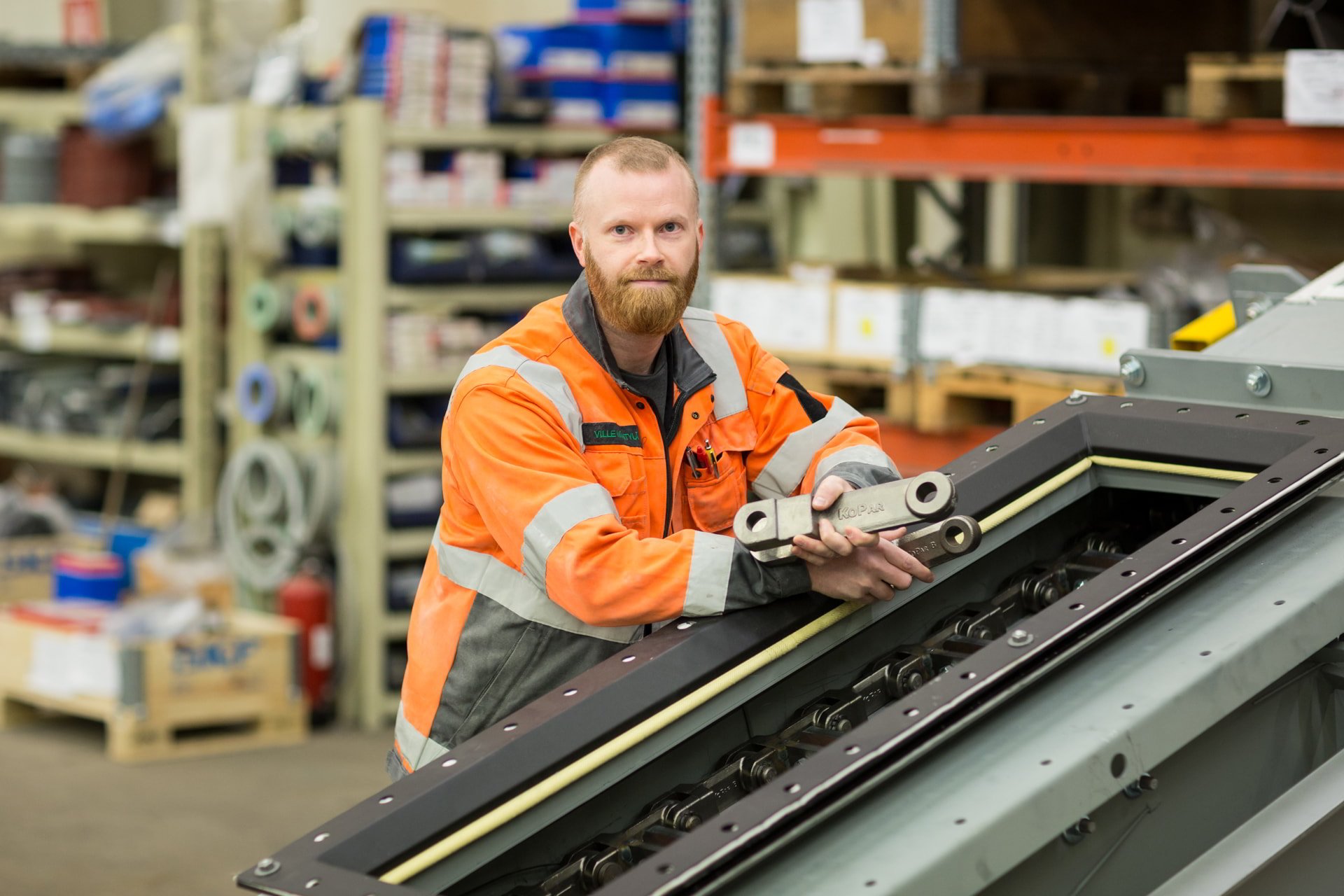
You have a challenge that needs solving?
Let us help! Contact us for more information about our products and services.