What is a drag conveyor and a scraper conveyor?
Drag conveyors and scraper conveyors are essential devices in industrial material handling, especially in the transportation of hot ash. These conveyors enable the efficient and safe transfer of large amounts of bulk material. Drag conveyors and scraper conveyors are often synonymous, as they perform the same function, although there may be slight differences in their structure. Both conveyor systems operate in closed channels, reducing the spread of dust and splashes in the work environment.
A scraper conveyor, also known as a drag conveyor, consists of a chain or belt to which scrapers or flights are attached. These scrapers move the material inside the channel, allowing for continuous and efficient material transfer. This makes the scraper conveyor an excellent choice for industrial processes where material transfer is critical to production flow. Scraper conveyors can also handle extremely hot materials, such as hot ash, which is particularly important in power plants, for example.
The significance of drag and scraper conveyors has been emphasized in many industries, as they offer versatility and cost-effectiveness. They can be used for both horizontal and vertical transfer, increasing their applicability in various environments. Such conveyor systems are also safe, as they reduce workers' exposure to hazardous materials.
How often does a drag conveyor need maintenance?
The maintenance needs of a drag conveyor depend on several factors, such as operating conditions and the type of material being transported. Generally, drag conveyors require regular maintenance to maintain their performance and durability at optimal levels. The frequency of maintenance can vary, but it is recommended to perform inspections and maintenance procedures at least once a year, or more often if the conveyor is used in particularly demanding conditions.
Maintenance intervals are influenced by factors such as the abrasiveness and temperature of the material being transported. For example, extremely hot or abrasive materials can wear out conveyor components faster, increasing maintenance intervals. Regular maintenance also helps detect potential problems early, which can prevent more significant damage and reduce downtime.
Common maintenance practices include inspections of the conveyor chain condition, lubrication, and cleanliness of the conveyor channels. In addition, it is important to ensure that all fastenings and protections are properly in place so that the conveyor operates safely and efficiently. By following these maintenance practices, the lifespan of the drag conveyor can be significantly extended.
What are the most common maintenance procedures?
The maintenance of a drag conveyor involves several key procedures that ensure the device's optimal operation. One of the most important procedures is the inspection and adjustment of the conveyor chain. The chain must be appropriately tensioned, as a chain that is too loose or too tight can cause excessive wear or even damage. Lubrication of the chain is also important, as it reduces friction and extends the chain's lifetime.
Another critical maintenance procedure is cleaning the conveyor channels. The accumulation of dust and splashes in the channels can impair the conveyor's performance and cause blockages. Regular cleaning ensures that the material moves efficiently through the channel and reduces wear. Keeping the channels clean is particularly important when handling hot ash or other abrasive materials.
Additionally, it is important to inspect and, if necessary, replace conveyor components, such as scrapers, flights, and fastenings. These parts are in constant contact with the material and can wear out quickly, especially under heavy use. Regular inspection and replacement of components help keep the conveyor operational and reduce downtime.
How to ensure the long service life of a drag conveyor?
The long service life of a drag conveyor can be ensured by following best practices and recommendations focused on preventive maintenance. Preventive maintenance means that the condition of the conveyor is continuously monitored, and potential problems are fixed before they cause more significant damage or downtime. This approach reduces downtime and extends the life of the conveyor.
One of the most important preventive actions is a regular inspection programme. The program allows monitoring of the condition of the conveyor chain and other components, helping to detect wear or damage in time. The results of the inspections should be carefully documented so that any necessary actions can be planned and implemented effectively.
Another key factor is staff training. It is important that the conveyor operators and maintenance personnel are well informed about its operation and maintenance requirements. Trained personnel can identify potential problems in time and perform necessary maintenance procedures correctly. This ensures that the drag conveyor operates efficiently and safely throughout its lifecycle.
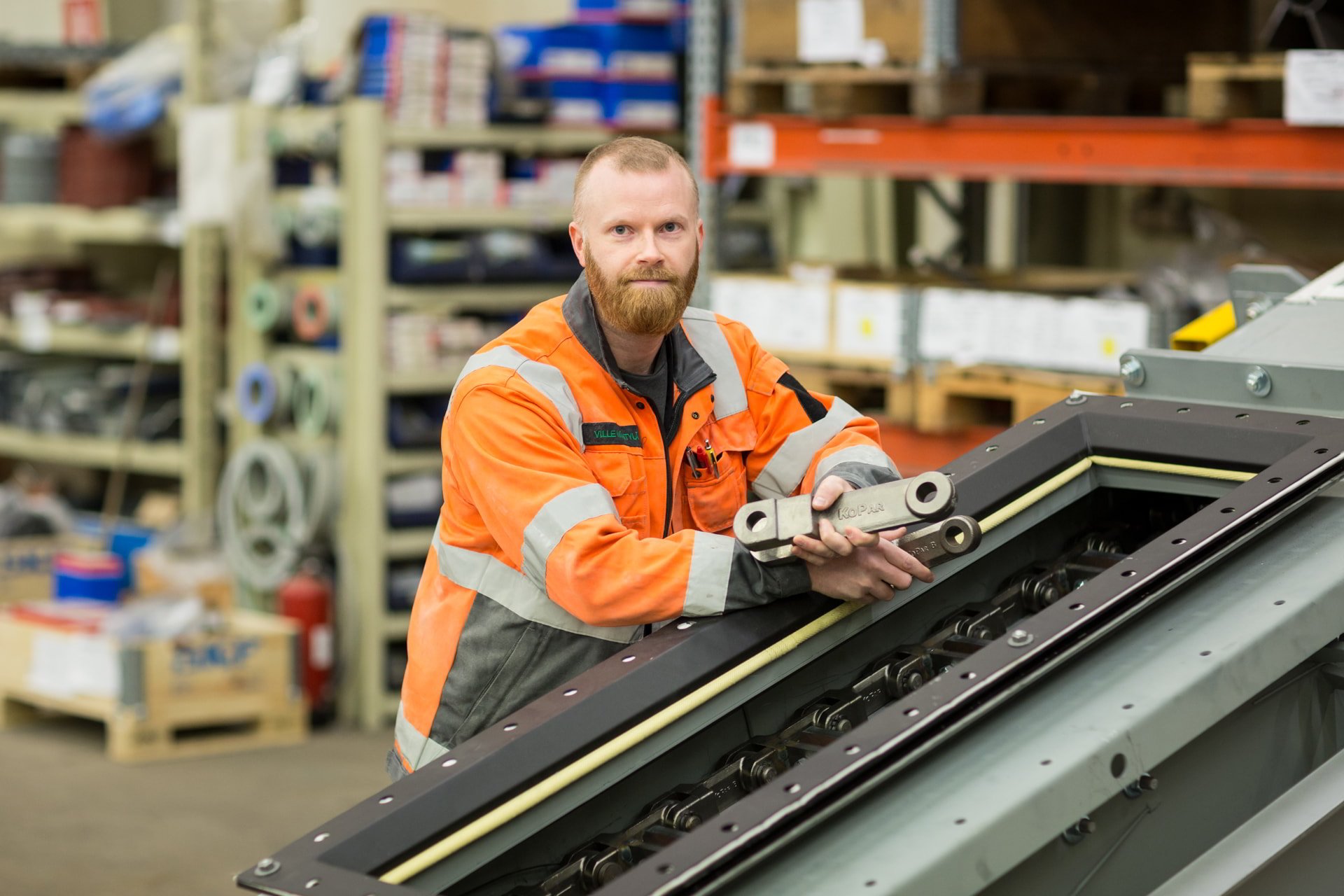
You have a challenge that needs solving?
Let us help! Contact us for more information about our products and services.