Essential Role of Forged Conveyor Chains in Material Handling
Forged conveyor chains are the backbone of many industrial processes, providing a reliable means of transporting materials across various stages of production. These chains are designed to withstand the rigors of heavy loads and continuous operation, making them an indispensable component in the process industry. The unique demands of conveying solid materials, especially those that are hot, abrasive, or dusty, require a robust solution that can maintain performance without frequent downtime for maintenance or repair.
We specialize in creating conveyor chains that are tailored to meet the specific needs of our clients' operations. By considering factors such as the type of material being transported, the environment in which the chain will operate, and the desired capacity, we ensure that each chain is optimized for its intended application. This customization is crucial for maintaining efficiency and reducing operational expenses over the life of the equipment.
Industrial Applications Requiring High Durability
In industries where materials are subjected to extreme conditions, such as high temperatures or corrosive environments, the quality and resilience of conveyor chains are paramount. Our chains are designed to last in the toughest of conditions, with materials like boron steel offering multiple lifetimes compared to traditional manganese steel. This not only ensures continuous operation but also translates to significant savings in maintenance and replacement costs.
For applications that involve harsh chemical conditions or continuous operation at elevated temperatures, we provide chains made of specialized materials such as stainless steel and heat-resistant steel. These materials are selected to maintain the integrity of the chain in environments that would quickly degrade lesser materials, ensuring that your process runs smoothly without the risk of unexpected downtime.
Customization for optimal performance
The customization of conveyor chains is not limited to the selection of materials. The design of the chain itself, including the type of link, the amount and location of flights, and the pitch of the flights, is tailored to the characteristics of the material being conveyed. This level of customization is what sets us apart, as it guarantees that the chain not only meets the demands of your process but does so with the lowest possible operational costs.
By providing chains that are assembled to order, we ensure that each component is ideally suited for its role. This attention to detail is a key factor in achieving the lowest total cost of ownership for our clients. It's not just about the initial purchase price; it's about creating a solution that will deliver reliable performance over the long term, reducing the need for costly interruptions and replacements.
Proactive Maintenance for Uninterrupted Operations
Anticipation and proactive maintenance are critical in keeping drag chain conveyors running efficiently. We have developed practical tools to measure chain elongation, allowing for easy and frequent monitoring. This process helps to maximize the chain's service life and minimize the risk of breakage and unplanned maintenance. By recommending chain replacement at the appropriate time, we help ensure that your operations continue without interruption.
The replacement of sprockets alongside the chain is another practice we advocate for optimal operation. This ensures that all components of the conveyor work in harmony, reducing wear and extending the life of the system. Our commitment to continuous improvement in design and maintenance practices is a testament to our dedication to providing durable solutions that keep your processes running smoothly.
Meeting the Challenges of Conveying in the Process Industry
The process industry presents a unique set of challenges when it comes to conveying materials. Our drag chain conveyors, screw conveyors, elevators, and excavators are engineered to handle these challenges with ease. Designed for versatility, they can accommodate steep inclination angles and are capable of operating in difficult environments, including those with high temperatures or abrasive materials.
Our solutions are not only robust but also versatile, capable of handling large capacities of up to 300 tonnes per hour. The modular design of our systems allows for installation in a variety of settings, ensuring that no matter the complexity of the environment, we can provide a conveying solution that meets your needs. This adaptability is crucial for industries that require reliable material handling under demanding conditions.
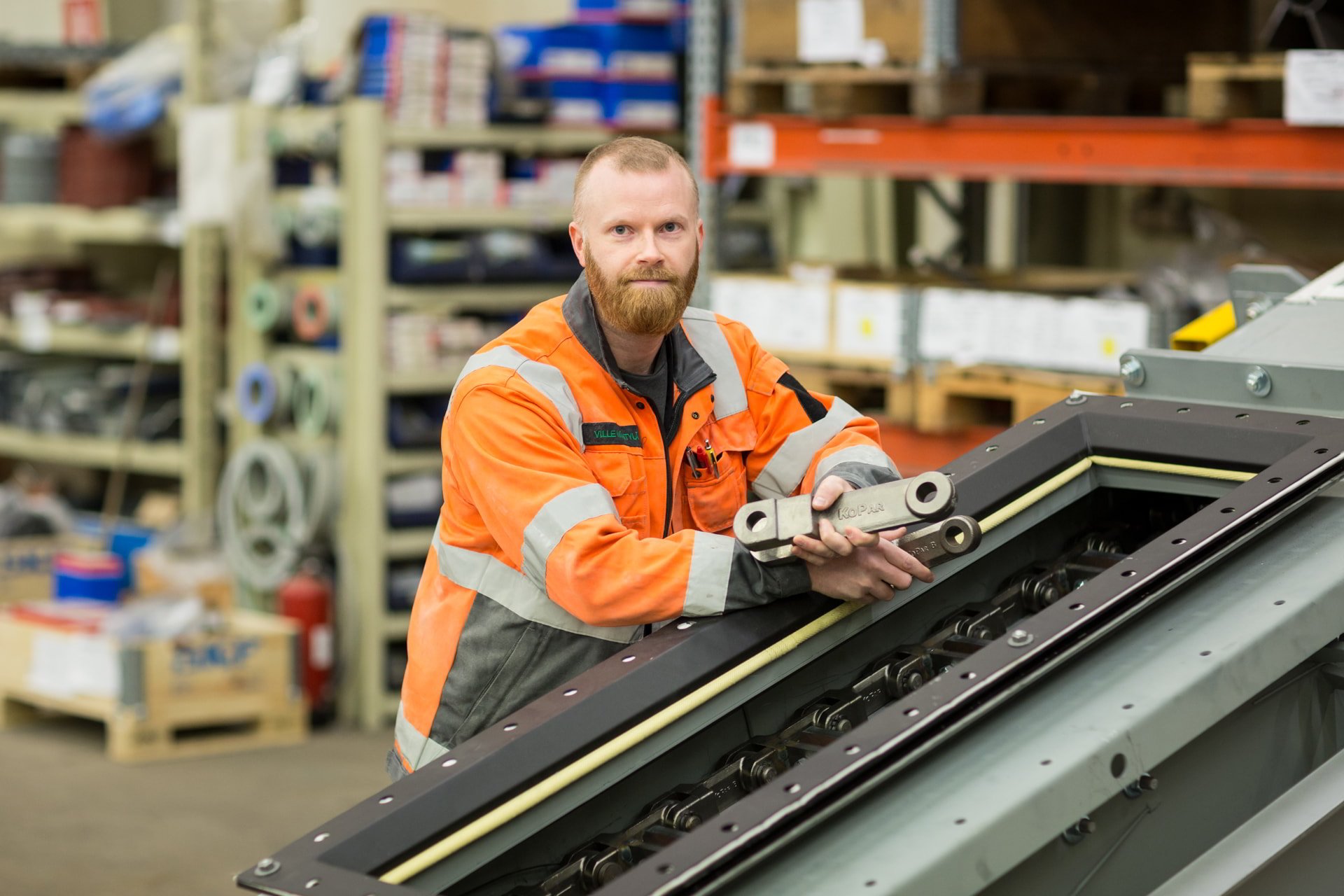
You have a challenge that needs solving?
Let us help! Contact us for more information about our products and services.